APA conducts five-yearly gas surveys for all of the gas pipelines that it operates within the Adelaide and regional South Australian distribution networks.
This includes approximately 7,700 km of predominately steel and polyethylene mains, 90 per cent of which are located under council footpaths with 10 per cent under roads.
A number of different companies were invited to demonstrate their infra-red laser detection products to APA technicians and engineers and, after a thorough investigation, Street Evaluating Laser Methane Analyser (SELMA) was selected.
Old school revolution
Prior to the introduction of SELMA, each field technician could only survey approximately 8 km of pipelines per day.
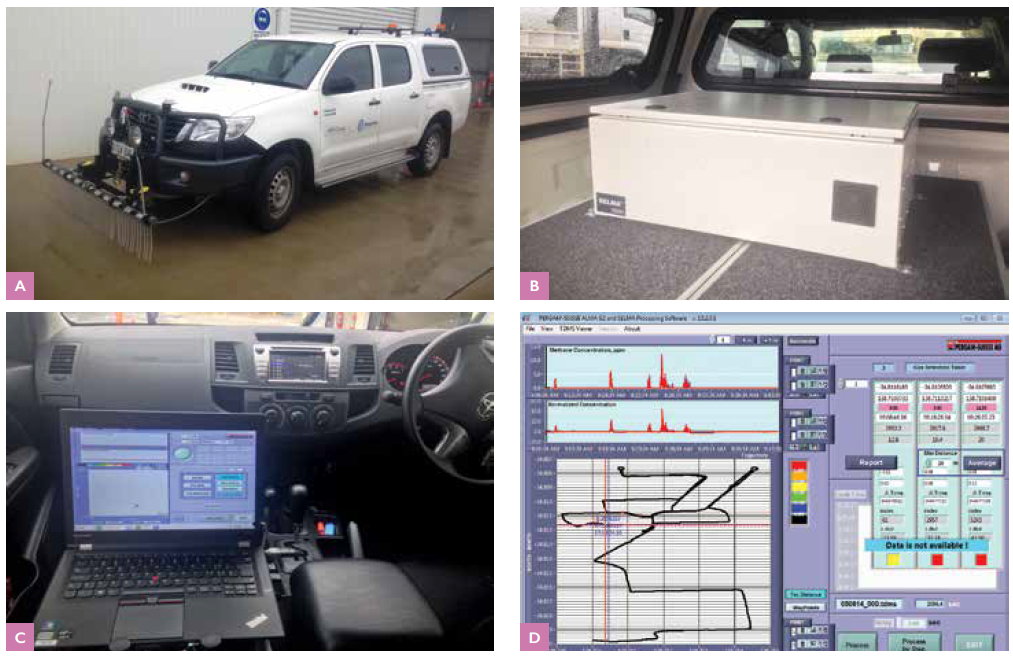
- A. Tubes mounted to the front of the detection vehicle.
- B. A SELMA unit mounted in the rear of the detection vehicle.
- C. A laptop mounted in place of the front passenger seat.
- D. Example of the SELMA laptop display.
SELMA (Street Evaluating Laser Methane Assessment), mounted on cars is a gas leak detector. The main applications of the system are the leak detection on natural gas transport and distributions pipelines, inspections of methane tanks, compressor stations and other potential sources of methane emissions to the atmosphere. The working principle of this methane gas leak detectors is based on a pulsed beam from a diode laser.
These surveys were done using driven and pushed buggies fitted with gas detectors and sometimes even technicians carrying gas detectors walking the length of the survey route. These gas detectors used the traditional flame ionisation detection process to find gas leaks. Air was pumped into the gas detector and mixed with oxygen and hydrogen, where a flame jet was then ignited and a combustion reaction takes place.
Carbon ions produced in the reaction are collected in a cylindrical shaped collector and a current passing through the carbon ions is then compared to an initially calibrated signal to determine the amount of gas present.
Moving with the times
In the last decade a new infra-red gas detection technology has been adopted in the oil and gas industries, and is proving itself a reliable and suitable replacement for flame ionisation. With infrared detection, a transmitter sends a laser beam of a specific wavelength through air to a receiver.
Only methane gas can absorb the laser at this specific wavelength, therefore, if methane is present in the plume between the transmitter and the receiver, some of the laser energy will be absorbed and its intensity will decrease.
The intensity of the received signal is compared with the intensity of a reference calibration signal to determine the amount of methane in the plume. As methane makes up 95 per cent of distributed natural gas, it is suitable for detecting natural gas.
Infra-red detection doesn’t require any pumps or calibration gases and is self-calibrating, therefore it requires less maintenance than flame ionisation equipment. False alarms are reduced with infra-red detection while flame ionisation can be sensitive to organic gases if the survey is conducted near a farm or a food processing plant for example.
How it works
Air sampling is done using a number of small plastic tubes connected to a main tube mounted to the front bumper of a vehicle.
The air is then filtered and routed using vacuum tubes into a medium between two reflecting mirrors where the laser is emitted and reflected to analyse the gas sample, when after the gas is analysed it is exhausted out of the SELMA unit.
The SELMA unit consists of the pump, laser, mirrors and laptop, which is mounted in place in the passenger seat, for processing the analysed data.
The field technician monitors the graphical readings on the laptop while the data is being saved and plotted as the vehicle drives along the survey route at speeds of up to 50 km/h.
This equipment is capable of surveying the gas main and inlet services in one run and gives an indication (visual and audible) of a leak within a 10-20 m radius. To accurately locate and classify the leak, the driver parks the vehicle in a safe spot and uses GMI gas detection equipment.
SELMA’s detection threshold level is adjustable and small methane detections related to sewerage gas, rubbish bins or other background methane can be eliminated without losing the original data.
Installation of the SELMA unit and in-field training took approximately two weeks and the unit has been used by APA Group’s South Australia Networks team since November 2013.
The advantages of the system:
- Low maintenance
- Only detects methane
- Detection at high driving speeds Remote detection
- Easily installed in most vehicles
- Simple operation and data assessment
The SELMA system consists of two individual units which can be used simultaneously or as one unit depending on user preference:
- Roof mounted remote detector – “SELMA Roof” remote detector.
- Front mounted local detector – “SELMA MPB” Local detector.
Compared to previous leakage detection methods, SELMA has delivered the following benefits:
- The average length of pipeline surveyed has increased from 8 to 30 km/d
- Improved safety for the field survey technician – avoiding driveways, road intersections and hot weather
- Reduced physical fatigue to field technicians, as less walking is required
- Survey path and leak locations are recorded on Google Maps and can be displayed via the on-board laptop
- Stored survey path and leak locations can be retrieved and used as evidence for regulatory compliance
The successful implementation of SELMA within APA Group’s South Australia network has generated interest from other gas asset operators, prompting APA to conduct a demonstration. All who attended this demonstration, including operators from New Zealand, were impressed by the technology.
The Australian Pipeliner | February 2016