The purpose of this inspection is to obtain information about possible defects in the cover, detect differences in the landfill, and in the future even calculate annual emissions. After conducting several tests, the outcome turned out to be interesting. This encouraged them to fly into an entire landfill site to be able to carry out a detailed and accurate analysis. 24 flights in approximately 25 minutes each were performed to measure the area in a flat area. In total, they recorded about 55,000 measuring points in three days. After collection, this data was processed into very highly detailed emission maps. In addition, an orthomosaic was obtained of the current situation of the landfill.
Minimized disturbances with true terrain following
2 different ways of data collection were carried out. The yearly fixed route to measure methane was compared with the route with our drone equipped with a methane sensor. It was not a straightforward process since PPM-m was measured from the air and only PPM on the ground. However, during flying, disturbance of the measurement due to height differences and changing movements in the flight line such as curves must be taken into account. True Terrain Following sensor, which actively controls the drone so that it performs the flight as optimally as possible, helped to minimize these disturbances.
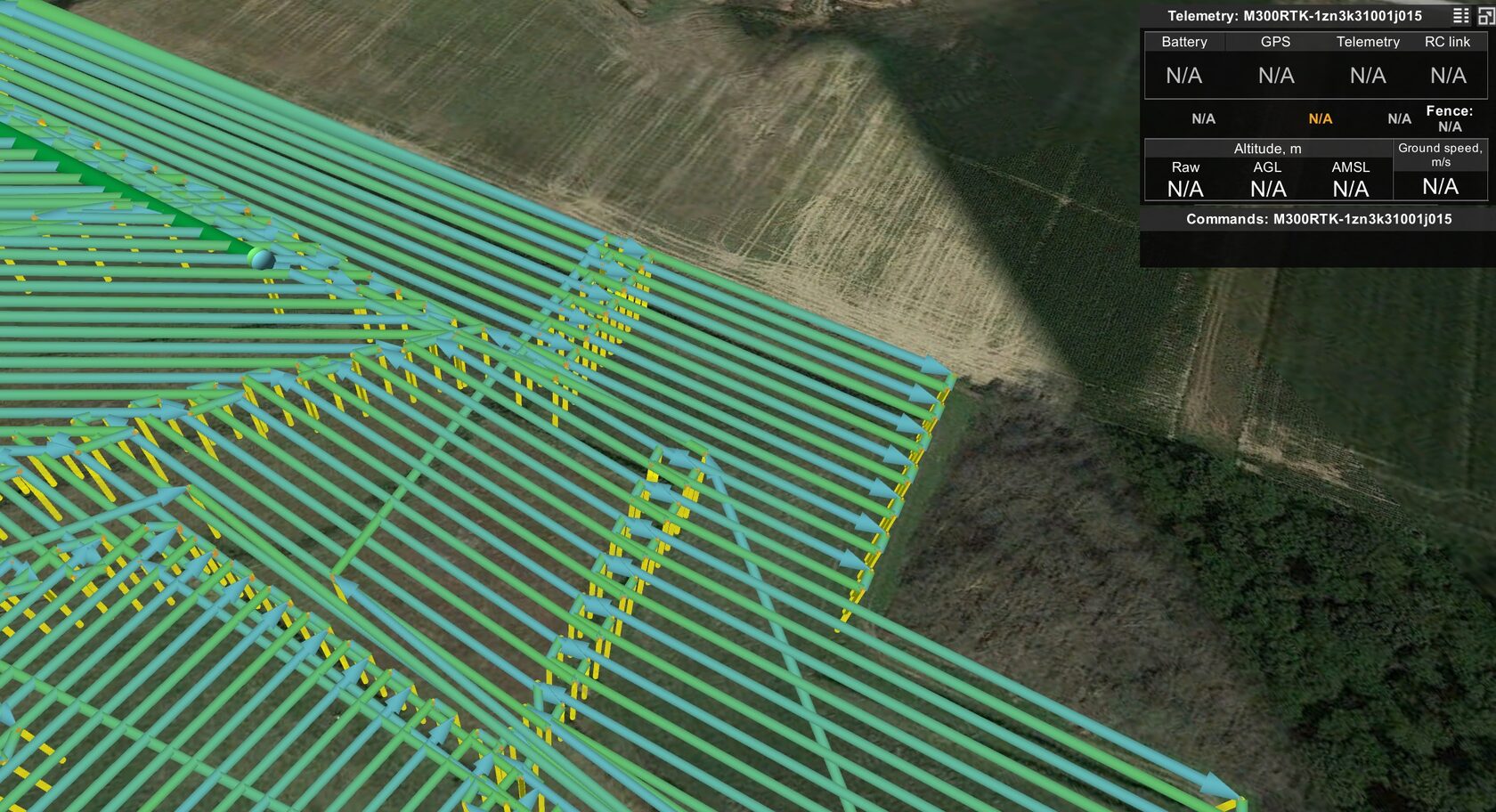
Combined effect of complex machinery, toolset and software
The system consists of the DJI M300 drone, SkyHub onboarded computer, Pergam Falcon methane sensor, and UgCS Software. For post-flight analysis, SkyHub records GPS-coordinated methane measurements on an SD card. UgCS offers precise flight planning skills at low altitudes in complex terrain. The software records Full Motion Video (FMV) with methane readings and instantly shows methane detections to the pilot. A GIS environment combines all processed data. This uses the orthophoto as a base layer on top of which other information, such as flight paths, measurements, emission maps, and presence of technical infrastructure, can be presented.
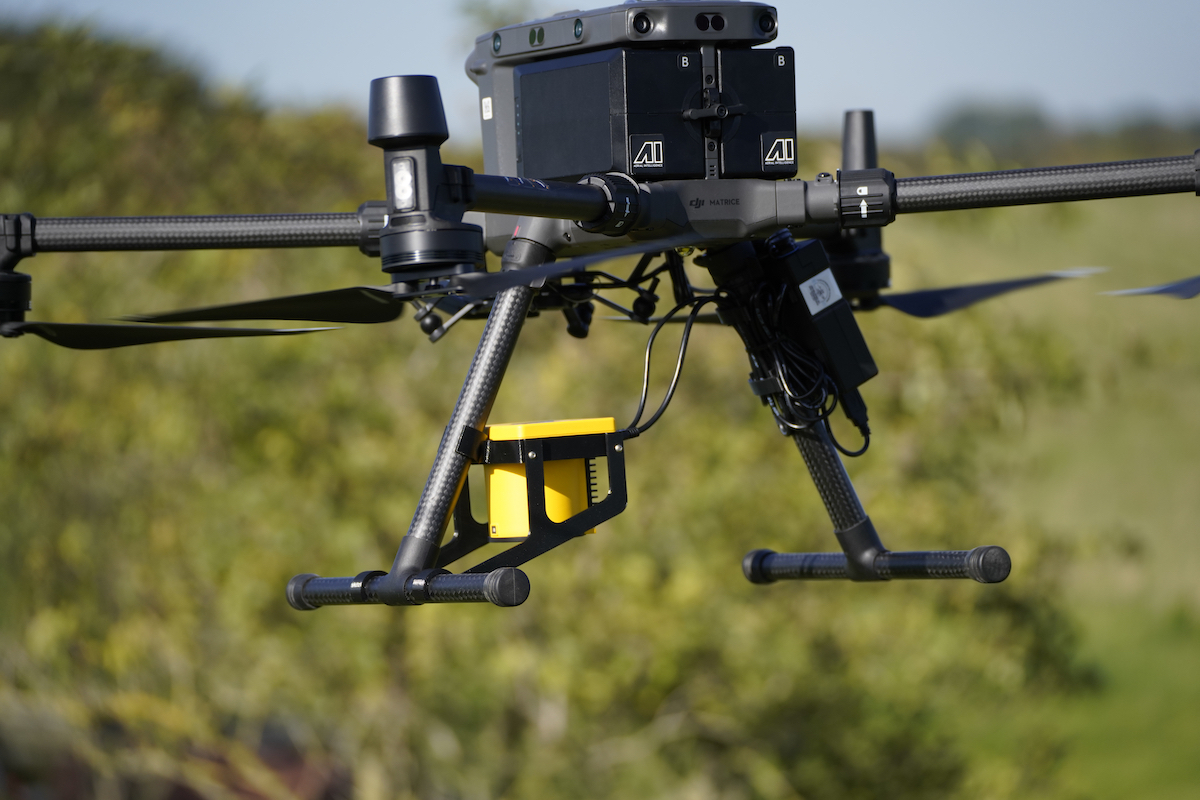
Flexible last-minute scheduling
The setup of M300 - Falcon Sensor - TTF - UgCS has empowered automated flights to be performed across the entire area of interest in a reasonably short length of time. It enabled the standardization of data collecting and lower noise by incorporating a methane sensor on a drone. It is convenient to have flexible last-minute scheduling options for the aircraft because the inspection of methane emissions depends on a variety of variables. The inspection of methane emissions is a very complex process that must take into account several variables, including the temperature and pressure in which the aircraft operates. This means that a plane’s flight schedule may need to be altered in order for it to undergo an inspection at any given time.
With this configuration, it was possible to collect data from around 55.000 points over a total area of over 30 hectares.
“To gain experience, we conducted many tests and mastered the technology. We did this by performing tests in controlled environments, after which we always adjusted 1 parameter. We compared the results of this and then included them during the data collection for this project. Overall, we are very positive about using this combination of technologies. It enables us to collect data efficiently, accurately, securely, and carefully, ” comments Nick Cornelissen from Aerial Intelligence.
The use of UAV-based data collection in relation to measuring methane emissions is a relatively new methodology. However, it has shown to be a very effective method of detecting methane leaks.
link to the original source